Application of non-destructive ultrasonic testing for metal castings and developing Indian foundry workers’ skills
Lead | University of Northampton |
REF Panel | B – Physical sciences, engineering, and mathematics |
UoA | 12- Engineering |
Location | India |
Funders | European Commission (EC), Royal Academy of Engineering |
Funds or grants | 7th Framework Programme for European Research Area, Newton-Bhabha Fund |
Partners | In India: Hindustan Institute of Science & Technology, INDSAT Corporation |
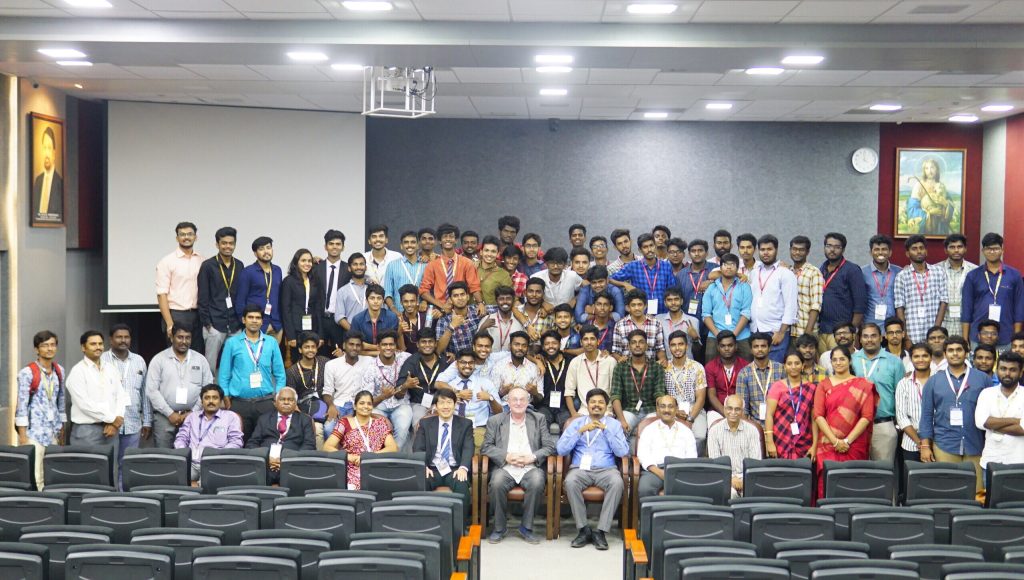
“All the Indian stakeholders, including workers, and company managers, showed their active participation in building the training programme … about 50-60% of the contents was customised by them. After that, each meeting led to fine tuning and to many iterations of the training materials purely based on industry requirements.” LMIC-based researcher
As the second-largest metal casting producer, India urgently needs to upgrade casting inspection processes and address a shortage of skilled foundry workers. UK-based and Indian researchers collaborated with industry partners to create a non-destructive, cost-effective, and potentially automated technique for measuring and testing casting components. The project also included specialised training and skill development for foundry workers to address capacity gaps in Indian foundries capable of using this laser and ultrasonic 3D scanning system. The results of this research helped the Indian metal sector to meet industry quality standards and reliability for increased business capacity.
Key Impacts
Innovative testing casting technique
- New non-destructive testing method enabled the generation of a 3D computer model, helping foundry industries improve the quality and efficiency of casting, and leading to increased automation in the inspection process. The new technique, adopted by 17 Indian foundries, is more environmentally friendly as it reduces approximately 20% of metal components waste and reduces 12% of money spent to dispose of rejected components. It has the potential to lead to further automation in the inspection process of manufactured castings.
Specialised training to meet global quality standards
- Researchers developed a locally–led training programme with industry partners, upskilling 76 foundry technicians and supervisors in the new technique, which meets ISO energy and environmental management requirements and standards of the American National Standards Institute, and American Society of Mechanical Engineers.
Sustainable partnership strengthening
- Hindustan University developed a new foundry skilled development centre to continue long-term training. The University of Northampton created a BSc (Hons) course on non-destructive testing.
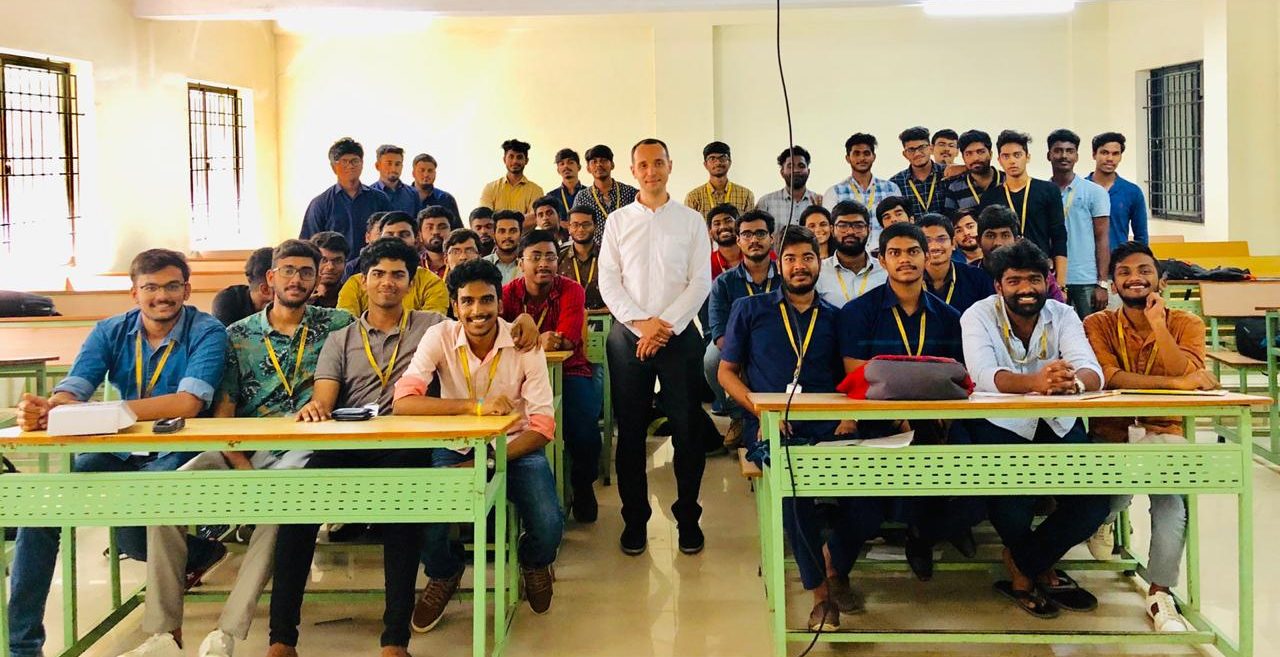
Underpinning research enablers
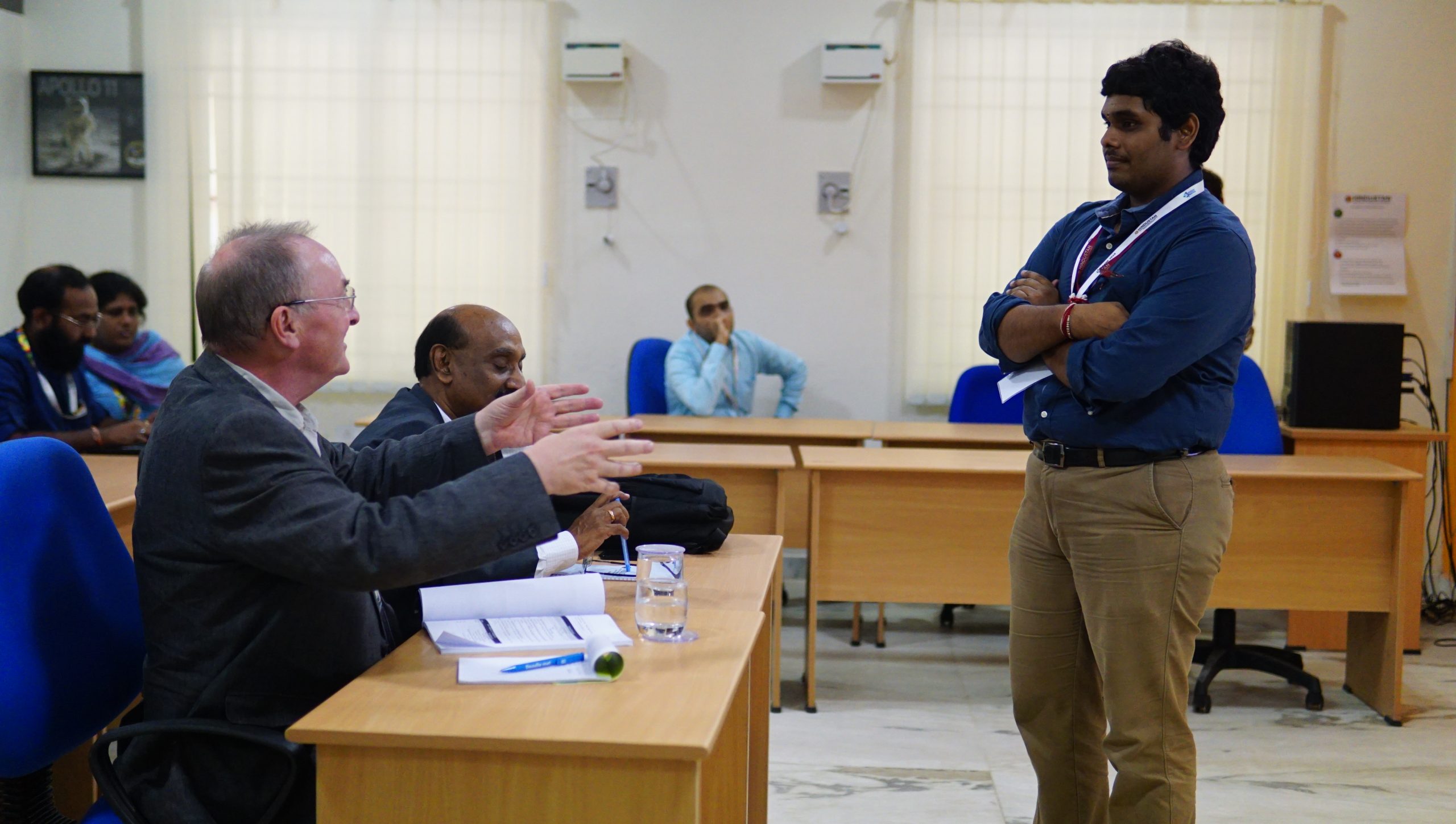
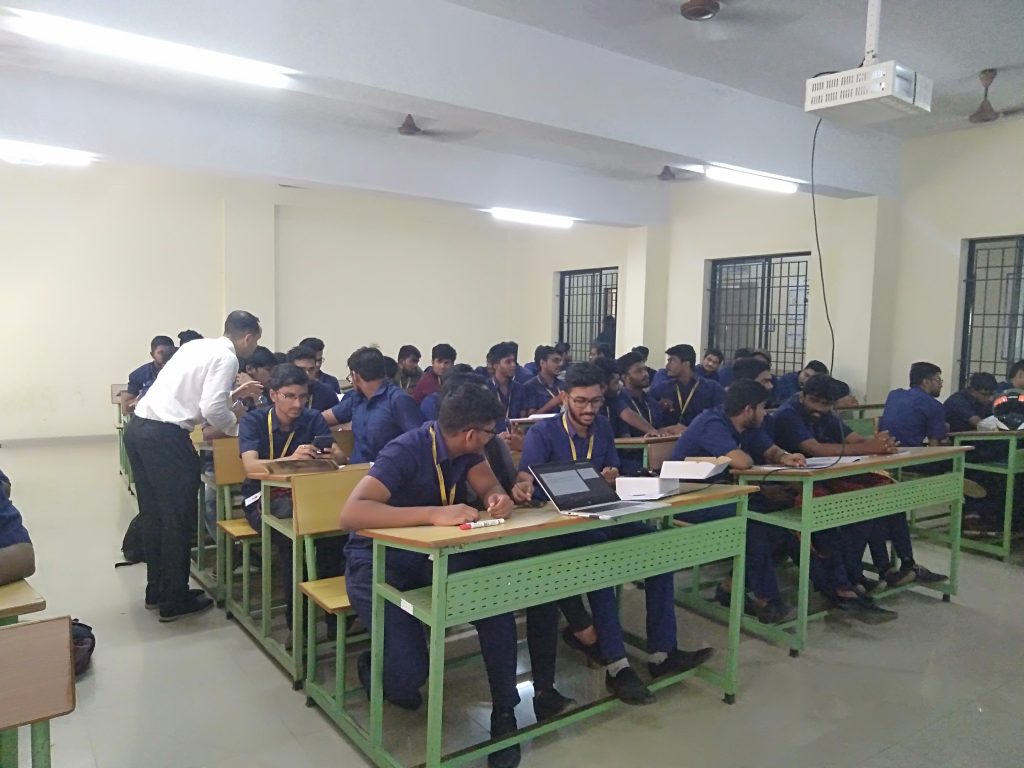
User involvement and ownership over research process and outputs
- Ensuring adequate contextualisation through early conversations with research users: By actively involving industry partners and seeking their input through initial surveys and discussions, researchers ensured that the project addressed specific local industry needs (e.g., skill shortage in modern inspection technologies).
- Expanding research uptake: Industry workers actively contributed to contextualising the training materials including translating them from English to Tamil. This enhanced the training program’s local relevance, gave continuity to user engagement, and enabled a broader audience to benefit from the training.
- Help in overcoming challenges: Committed company managers leveraged existing relationships to organise the training program during weekends and found a suitable location near multiple industries. They also provided sample materials for educational purposes. Industry support ensured greater accessibility and participation from industry workers and a hands-on training approach.
Multi-way continuous learning processes across all partners and disciplines
- Fostering an open and active communication channel: Regular in-person visits and online meetings between collaborating academic and non-academic partners enabled a dynamic research environment where insights, challenges, and discoveries could be exchanged. This led to a deeper and shared understanding of the project’s expected outcomes.
- Academic relationships expanded the project scope: The projected impact ultimately expanded as collaboration between University of Northampton and Hindustan Institute of Science & Technology was extended to include research students and postdoctoral researchers. Interaction between the project team and students created a knowledge-sharing dynamic, enriching findings and inspiring follow-on projects.
- Shaping outcomes through collaboration and inclusiveness: 17 Indian industries contributed to the design and delivery of training materials, ensuring that the curriculum aligned with industry needs. This increased the practical relevance and applicability of new methods, facilitated knowledge dissemination to a wide range of metal industry actors and, ultimately, supported long-term impact.